Ever wondered how the sleek, crystal-clear glass in your windows is made? Float glass, the backbone of modern glazing, owes its flawless finish to a fascinating process. In fact, the Pilkington Process, developed in 1959, produces over 90% of the world’s flat glass today! It’s a game-changer that replaced the older, less efficient methods.
This blog dives into the art and science behind float glass. We’ll explore how it’s made, why it’s superior to plate glass, and the variety of options it offers for both homes and businesses. Whether you’re renovating or just curious about the materials shaping our buildings, you’re in the right place. Let’s get started!
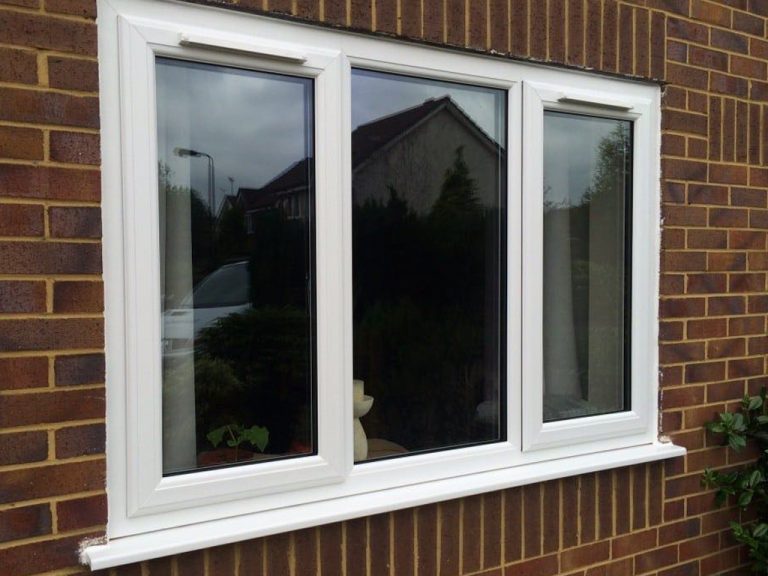
How Float Glass is Made
The manufacturing process of float glass is both intricate and fascinating. Known as the Pilkington Process, this method involves pouring molten glass from a furnace into a chamber filled with molten tin. Here’s a step-by-step breakdown:
- Molten Tin Bed: The molten glass floats on the tin, forming a flat and smooth surface as it spreads across the container’s width (ranging from 2.3 to 3.5 metres).
- Surface Formation: The glass’s top surface, also known as the air side or score side, is fire-polished, while the bottom, called the tin side, is not.
- Annealing in the Lehr: From the tin bath, the glass moves into an annealing oven (called a lehr) where it is gradually cooled. This critical step, known as annealing, relieves internal stresses, ensuring the glass’s durability and quality.
- Cutting and Finishing: Once cooled to room temperature, the glass emerges as a continuous ribbon. Automatic cutters trim and size the glass for various applications.
Plate Glass vs. Float Glass
Previously, plate glass was the standard for flat glass production. It involved grinding and polishing the glass to achieve a smooth surface. However, plate glass has been phased out due to safety risks when broken and its poor energy efficiency. The advent of float glass in 1959, perfected by Pilkington Brothers Ltd., revolutionised the industry, offering a safer and more efficient alternative.
Types of Float Glass
Two primary types of glass are produced using the float process: clear glass and tinted glass.
Clear Glass:
- Transparent and colourless.
- Allows approximately 75 to 92% of visible light to pass through, depending on thickness.
Tinted Glass (Heat-Absorbing Glass):
- Achieved by adding colouring agents like bronze, grey, green, or blue to the mix.
- As thickness increases, the density of the tint reduces light transmittance, with values ranging from 14 to 83%, depending on the glass’s colour and thickness.
Attention to Detail: Matching Existing Glass
At GL Glazing & Window Services, we use float glass to match your existing panes seamlessly. This ensures consistency across your windows, preserving the aesthetic appeal of your property. If your windows have multiple panes, we meticulously select float glass to match the existing ones. This attention to detail is a hallmark of our service, ensuring your satisfaction with the final result.
Why Choose Float Glass?
Float glass’s smooth surface, durability, and clarity make it a preferred choice for residential, commercial, and industrial uses. Here are just a few of its benefits:
• Versatility: Ideal for windows, doors, decorative panels, and more.
• Durability: Engineered to withstand everyday wear and tear.
• Customisation Options: Available in various tints and thicknesses to suit your specific needs.
Need Expert Assistance? At GL Glazing Window Services, we specialise in high-quality glass solutions tailored to your needs. Whether it’s for your home or business in Smethwick, Birmingham, or across the West Midlands, we’re here to help.
Looking for “window services near me” or reliable glazing professionals? Contact us at 0121 429 7611 or 07970 903 666 for expert guidance and top-notch service. We’ll make your vision a reality with precision and care.